Hej! Na #mtbxcpl piszę o kolarstwie dzięki TOBIE!
Wspieraj mnie, żebym mógł dalej być blisko kolarstwa, robić relacje z zawodów, pisać i zarażać pasją.
Moja znajomość z braćmi Pyrka jest tak długa jak historia Syrenki CX, bo tak się jakoś złożyło że obaj byli obecni od samego jej początku. Już wtedy nie tylko moją uwagę przykuła dość nowatorska manetka, którą mieli zamontowaną w swoich rowerach. Szybko się okazało, że jest ich projektu i realizacji. To zresztą nie była jedyna kolarska rzecz, która wyszła z ich warsztatu pod szyldem Pyrkiewicz. Obaj bracia mocno związani z projektowaniem, Leszek specjalizujący się aktualnie w 3D, a Staszek eksperymentujący z różnymi materiałami i z pomocą młodszego brata przenoszący rzeczy z ekranu do rzeczywistości. W sezonie 2021 jeździł na stworzonym przez siebie przełajowym rowerze z bambusa, w tym sezonie przesiadł się na karbon.
Kilka dni temu w serwisie Behance Staszek opublikował opis i dokumentację z tworzenia roweru. Czas jednak na wersję dla polskiego czytelnika. A było to tak…
Jeślibyście zapytali mnie czemu robię własne ramy carbonowe to nie mam sprecyzowanej odpowiedzi. Pewnie zacząłbym coś bełkotać o pandemii, o tym, że sama jazda mnie już nudziła i, że całkiem się wciągnąłem w tematykę materiałów kompozytowych. Coś bym jeszcze wspomniał, że pół młodości spędziłem na modelarni a w dorosłym życiu wymęczyłem tytuł magistra inżyniera. Na grubo niezdrowa fascynacja customowymi carbonowymi ramami zaczęła się jakoś w 2019. Szybko jednak przechodząc do tego co mi się udało ostatnio stworzyć:
Rok temu kiedy zrobiłem ramę bambusową byłem całkiem z siebie zadowolony, ale czułem, że stać mnie na więcej. Wyciągnąłem wnioski i zebrałem wytyczne co do następnej ramy:
- carbonowy chainstay, który rozwiąże problem zmieszczenia przełajowej opony i blatu zębatki, co było trudne z użyciem prostych bambusowych tyczek
- mufa suportu w standardzie T47 zamiast pressfit’u. Chociaż pressfit działał u mnie dobrze i nie skrzypiał to dla wygody w przyszłości chciałem zastosować wkręcany wkład suportu
- carbonowe dropouty pod UDH zamiast aluminiowych
- mocowanie hamulca w standardzie flatmount zamiast postmount
- carbonowa rura podsiodłowa laminowana na rdzeniu – rozwiązałoby to problem pasowania sztycy
- carbonowy toptube z wypłaszczeniem na spodzie do wygody noszenia na ramieniu podczas pokonywania przeszkód na wyścigach przełajowych
Na pierwszy ogień poszła rura górna, ponieważ wydawała się najprostsza do zrobienia. Kształt z ergonomicznym wypłaszczeniem zaprojektował mój młodszy brat:
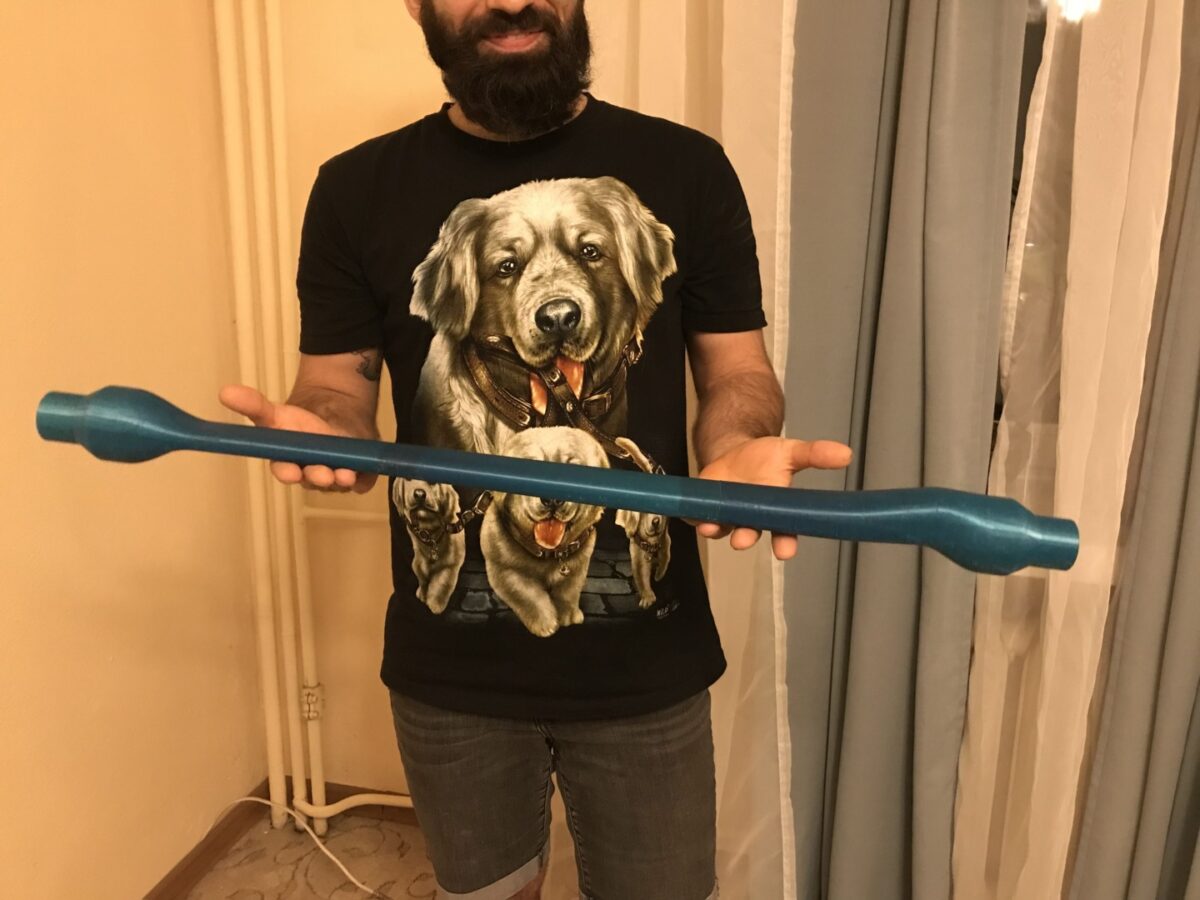
Niestandardowo w stosunku do wielkich producentów zdecydowałem się na podział w formie w kierunku horyzontalnym a nie w płaszczyźnie symetrii. Przecież jak będę siedział na nim i jechał to chcę widzieć ładny carbon a nie linie podziałową. Rurkę wydrukowałem w trzech częściach na mojej drukarce 3D.
Sklejony, wyszlifowany, zapodkładowany i pomalowany model umieściłem na podstawkach do których przykręciłem płytę, która służyła do stworzenia powierzchni podziałowej formy.
Na płycie z plasteliny technicznej ulepiłem piramidki, tak by pozycjonowały względem siebie obie połówki formy.
Model wraz z płytą podziałową pokryłem pięcioma warstwami wosku i przystąpiłem do procedury tworzenia form z laminatu: 2 razy żelkot i dalej sprawdzona kombinacja mat i tkanin szklanych przesycanych żywicą. Na koniec formę wzmocniłem bambusem.
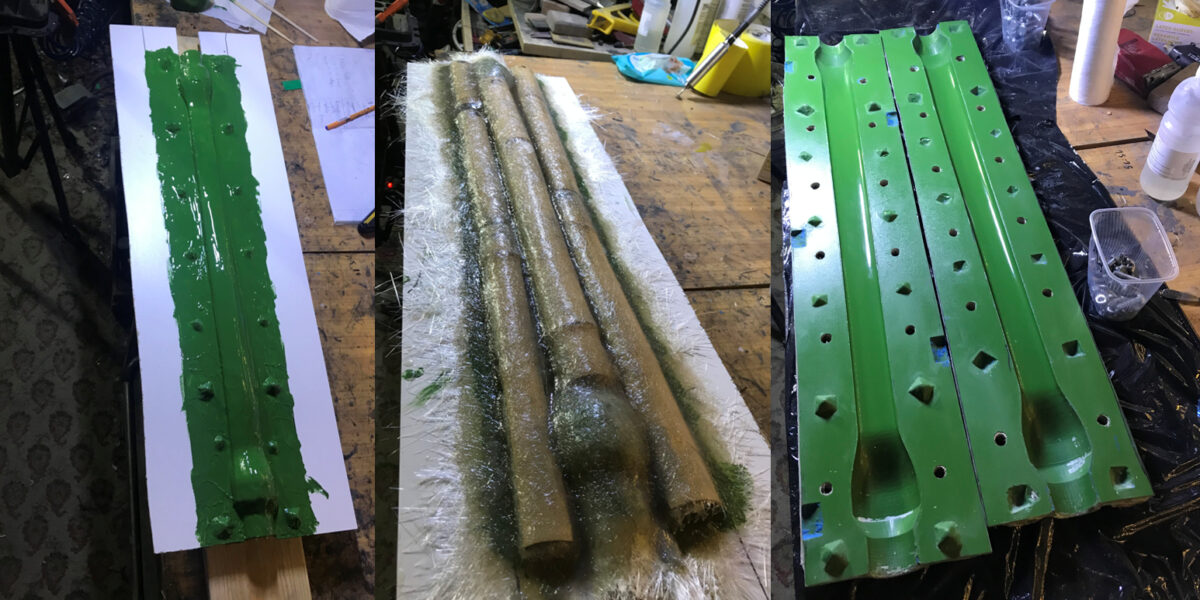
Korzystając z dobrodziejstw technologii „bladder moulding”, gdzie pompowany rdzeń dociska materiał do powierzchni formy udało mi się zrobić rurkę. Widać spora wypływkę żywicy, zbyt hojnie rozprowadzałem ją po warstwach węgla.
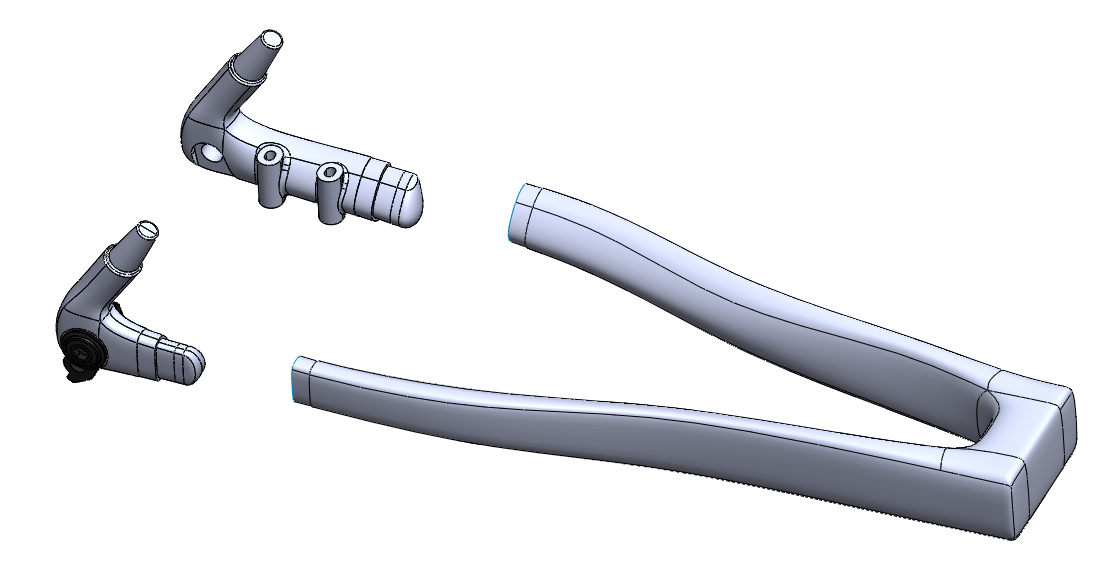
Cały „dolny tył” to projekt 3D brata. Ja oddzieliłem CS, które będzie robione w technologii bladder moulding od dropoutów, do których dostosuję lekko podrasowaną technologie compression moulding.
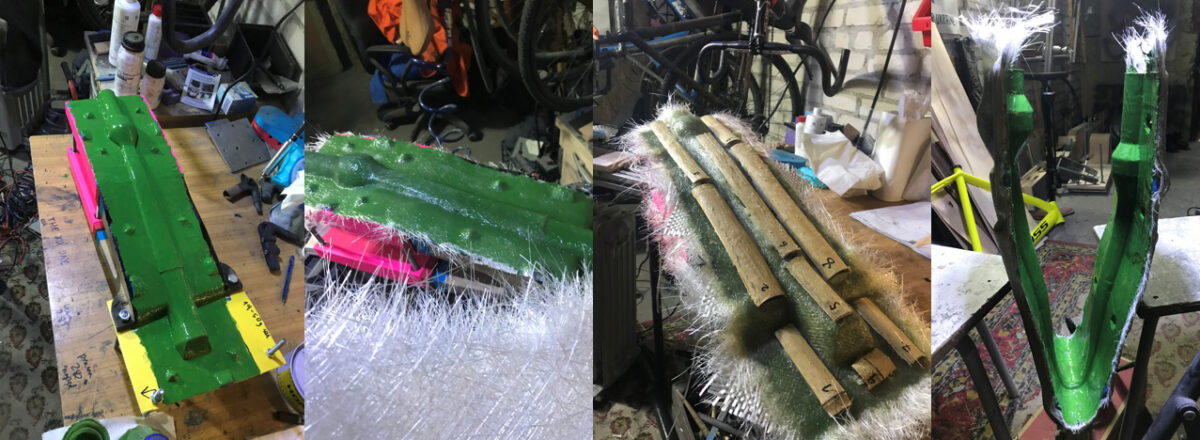
Po kilku iteracjach i spełnieniu moich wytycznych technologicznych doszliśmy do porozumienia. Tu np. jedna z poprawek jakie musieliśmy wprowadzić na modelu. Nalegałem, żeby forma była trzy częściowa – lewa, prawa i środkowa. Żeby możliwe było wysuniecie elementu ze środkowej części formy musieliśmy wyeliminować podcięcia. Długość 2 musi być mniejsza od 1.
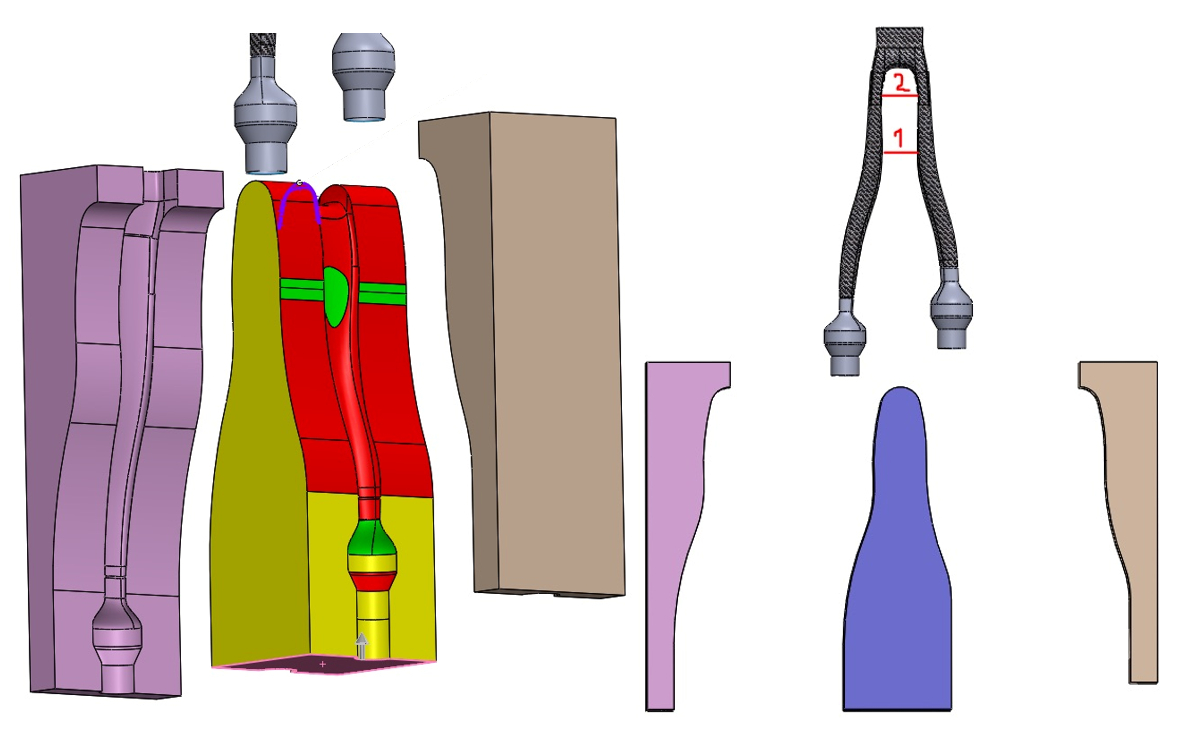
Wydrukowałem model wraz z powierzchnią podziałową. Z perspektywy czasu było to trochę szalone jeśli chodzi o ilość druku, ale dostałem akurat darmowe resztki filamentów i miałem covida, więc scenariusz na długie domowe drukowanie sam się napisał.
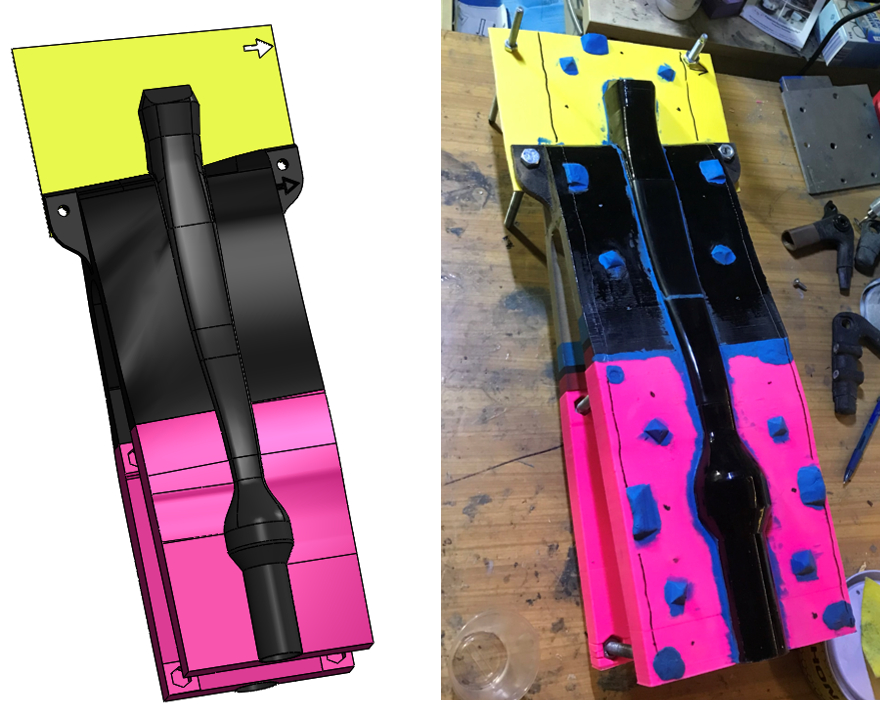
Wyzwaniem oczywiście było wylaminowanie środkowej formy, gdyż miejsca nie było dużo i z każdą dodawana przeze mnie warstwą robiło się go coraz mniej.
Ze względu na skomplikowanie tej formy zachowałem maksymalna ostrożność podczas pierwszego obciążania formy ciśnieniem.
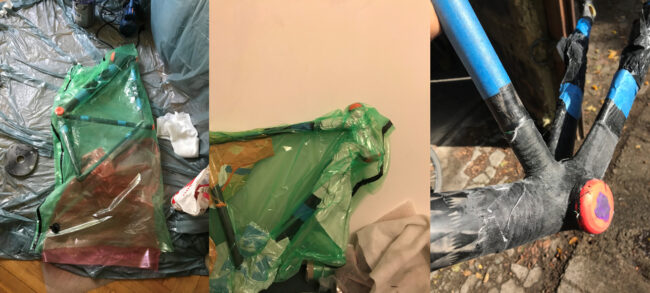
Nie jest to prosta cześć do wylaminowania bez użycia prepregów, ale za drugim podejściem efekt był zadawalający. Musiałem zrobić sobie instrukcję laminowania i dobrze wszystko przygotować żeby zdarzyć przed utwardzeniem żywicy. To była długa sobotnia noc z 17 na 18 czerwca, skończyłem koło 2:30.
Haki to zupełnie inna para kaloszy. Formę wydrukowałem z PLA.
Reszta to dość tajna technologia, której nie mogę tu opublikować. Napiszę tylko w ramach ciekawostek, że podczas zamykania połówek formy przez jej specjalne ukształtowanie oraz dodatkowe elementy ciśnienie na oblaminowany pod wymiarowy rdzeń wytwarzane jest z każdej strony. W kluczowych obszarach zastosowałem też włókno aramidowe. Na lewym haku pokusiłem się o followup do mojego innego projektu.
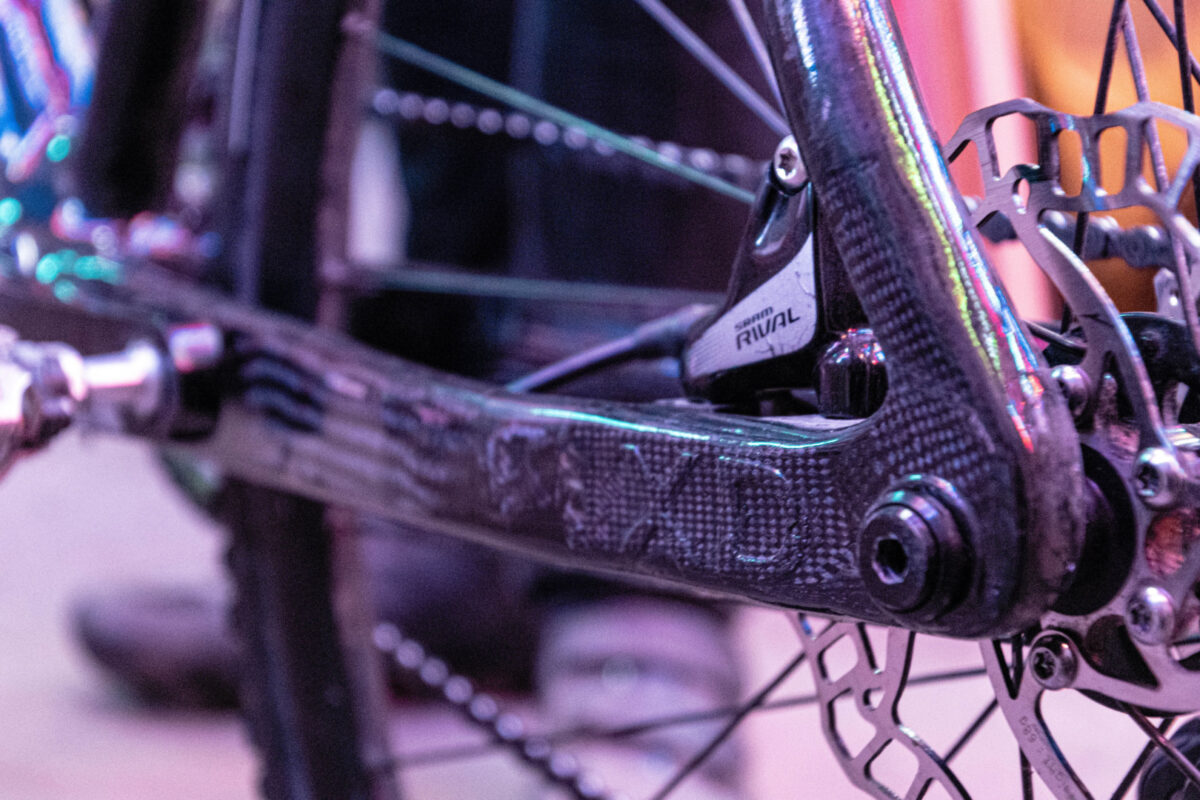
Oczywiście tulejki pod mocowanie hamulca były bezpośrednio wlaminowywane w hak, bez późniejszego klejenia.
Główka ramy, żeby zapewnić dokładne wymiary pod stery była laminowana na wytoczonym aluminiowym rdzeniu. Żeby umożliwić późniejsze zsunięcia elementu z rdzenia, wylaminowana główka na rdzeniu trafiła do pieca. Jako, że aluminium ma znacznie większy współczynnik rozszerzalności cieplnej od kompozytu po utwardzeniu i ostygnięciu do temperatury pokojowej stosunkowo łatwo jest ja zsunąć z rdzenia. Kompensacje wymiarową wzięto pod uwagę sporządzając dokumentacje rysunkową dla tokarza.
W sprawie toczenia miski supportu uśmiechnąłem się do kolegi Adama. To była długa i owocna współpraca :) Dzięki standardowi T47 możliwe jest użycie korby z osią o średnicy 30 mm i przeprowadzenie przewodów wewnątrz ramy
Czas nieubłaganie pędził, do sezonu przełajowego zostało jakieś 1,5 miesiąca. Do zrobienia miałem jeszcze rurę podsiodłową. Chcąc oszczędzić sobie pracy napisałem do firmy M.Carbo. Dostałem super ofertę na całą resztę rurek – podsiodłowa, dolną i seatstaye. Wtedy to nastąpiła wiekopomna przemiana – już nie robiłem liftingowanej ramy bambusowej z kilkoma rurkami carbonowymi tylko w pełni carbonową ramę. Wierzę, że to początek przyszłej współpracy. M.Carbo robi rurki w technologii filament winding nawijając rowing węglowy na rdzeń. Powstają z tego rurki o dobrych parametrach i oryginalnym wyglądzie. Podobne używają chociażby czeska Festka czy amerykanski Bastion cycles. Jak dobrze pójdzie ekipa z M.Carbo ma w najbliższym czasie przenieść produkcje z Białorusi do Polski.
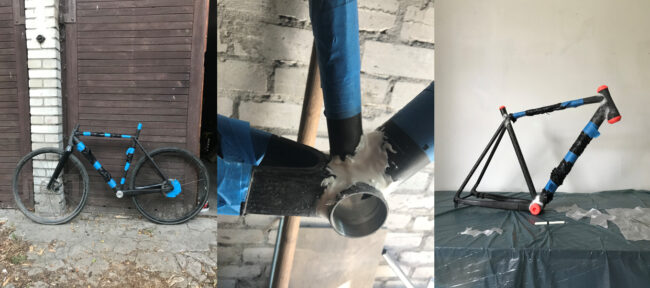
Do dopasowywanie rurek wydrukowałem sobie szablony, wszystko skleiłem na jigu.
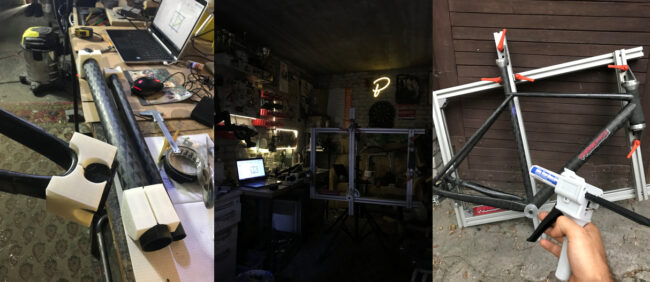
Szybkie sprawdzenie geometrii i na węzły nałożyłem lekką pastę zrobioną z żywicy epoksydowej, kleju i pustych w środku mikro kulek szklanych o gęstości 0,19 g/cm^3. Węzły następnie wyszlifowałem tak by łatwo było w kolejnym kroku je oblaminować.
Laminowanie węzłów to była niezła przygoda. Nie było czasu na dużo zdjęć.
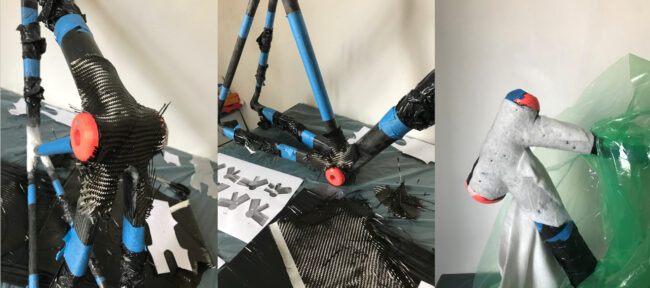
Po laminowaniu każdego z węzłów warstwy włókna węglowego przykrywałem przygotowywanymi wcześniej rozkrojami z delaminażu. To taka tkanina z nylonu, która służy do wchłonięcia nadmiaru żywicy i przygotowania powierzchni do dalszych operacji. Na delaminaż trafiał jeszcze breather, który również przechwytywał nadmiar żywicy a także pomagał równomiernie zapewnić docisk podczas utwardzania żywicy. Wszystko na jakieś 20 godzin trafiało do worka próżniowego.
Węzły zostały w kolejnym kroku zapodkładowane i pomalowane na czarno. Następnie całą ramę pokryłem lakierem bezbarwnym.
Zostało tylko poskładanie wszystkiego w całość i można było ruszać na objazd nowego rowerka.
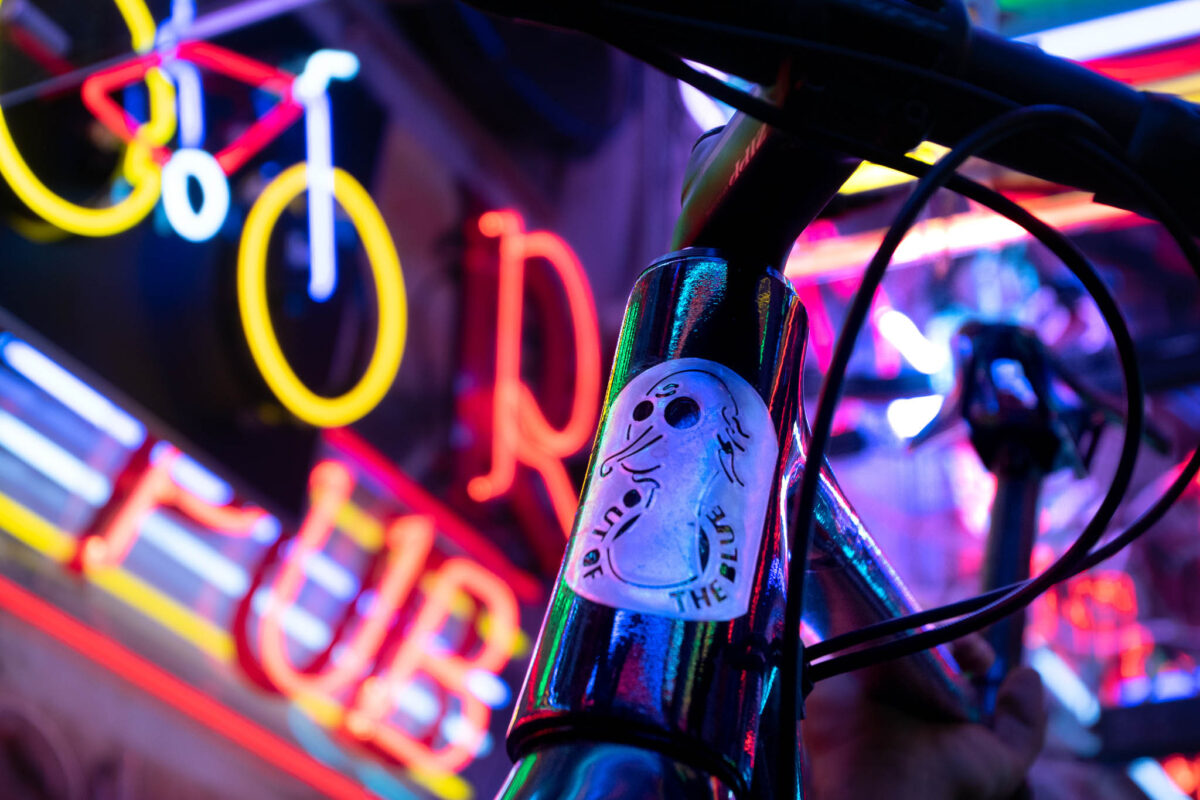
Pierwszy start przypadł na wyścig halloweenowy. Skorzystałem z tego zaopatrując się w duży dmuchany strój, który w razie jakiś defektów miał chronić mnie przed bolesnymi upadkami.
Kolejny start to już były poważniejsze zawody, drugi w sezonie wyścig Syrenki CX, na którym udało mi się zająć 7. miejsce na około 70 startujących.
Z kolei 10 grudnia na wyścigu towarzyszącym Pucharowi Polski w kolarstwie przełajowym w Cetniewie wjeżdża na 3. miejsce podium. Oto co mówił na mecie:
COMMENTS